KEYNOTE SPEAKERS
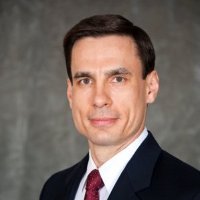
Volodymyr Babich
Professor of Operations and Information Management at the McDonough School of Business, Georgetown University
Go to the presentation slides
See the video of the keynote
Volodymyr Babich is a Professor of Operations and Information Management at the McDonough School of Business, Georgetown University. He was a Visiting Associate Professor at the London Business School, a Visiting Scholar at the University of Chicago Booth School of Business and Wharton School at the University of Pennsylvania, and an Assistant Professor at the University of Michigan, Ann Arbor. He earned his Ph.D. in Operations Research from Case Western Reserve University, Weatherhead School of Management. He holds M.S. degrees in Management Science and in Mathematics.
Prof. Babich’s research interests are the interface of operations and finance, supply risk management, supply chain management, energy and sustainability, entrepreneurship, innovative operations technologies, stochastic modeling, and risk management. His research has been supported by the National Science Foundation, and various university and industry grants. His papers have been published in the leading Operations Research, Operations Management, and Industrial Engineering journals. Prof. Babich serves as an associate editor for Management Science, M&SOM, and Naval Research Logistics, and as a senior editor for Production and Operations Management journals. He is an active member of INFORMS and the MSOM society and has served twice as the Chair of the MSOM Special Interest Group on the Interface of Finance, Operations, and Risk Management (iFORM).
Playing with DISASTER: a Behavioral Simulation Platform of Supply Shortages, Competition for Supplier Capacity, Blockchain-enabled Strategic Information Sharing, and Markets for Capacity-Token Trading.
Abstract Blockchain technology allows the creation of incorruptible records of a firm’s orders and the anonymous sharing of these records with other firms in the industry. Blockchain technology also facilitates the creation of markets among retailers for trading tokens that represent claims on the supplier capacity. Using the online platform we created (called DISASTER), we conduct behavioral simulations to study the effects of supply shortages, information sharing on supply shortages, and markets for supplier capacity. These experiments offer insights into the present and the future of supply chains: why supply chain shortages can persist even after the current capacity constraints are lifted, what information accelerates order inflation and the Bullwhip Effect, what trading strategies emerge in markets for supply chain resources, and how well clearing prices in these markets reflect the value of the supplier’s capacity for the retailers.
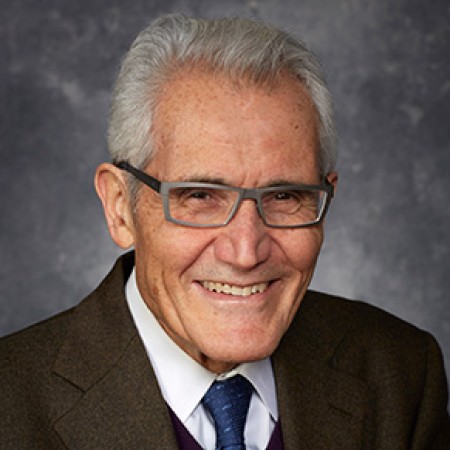
Alain Bensoussan
Professor of Risk and Decision Analysis
Lars Magnus Ericsson Chair
Go to the presentation slides
See the video of the keynote
Alain Bensoussan is Lars Magnus Ericsson Chair and the Director of ICDRiA (International Center for Decision and Risk Analysis) at the University of Texas at Dallas He is also Chair Professor of Risk and Decision Analysis at the City University Hong Kong. He has been for 4 years World Class University Distinguished Professor at Ajou University, Korea . He is Professor Emeritus at the University Paris Dauphine. Professor Bensoussan served as President of National Institute for Research in Computer Science and Control (INRIA) from 1984 to 1996; President of the French Space Agency (CNES) from 1996 to 2003; and Chairman of the European Space Agency (ESA) Council from 1999 to 2002. He is a member of the French Academy of Sciences, French Academy of Technology, Academia Europaea, and International Academy of Astronautics. His distinctions include AMS Fellow, IEEE Fellow, SIAM Fellow, Von Humboldt award, and the NASA public service medal. Professor Bensoussan is a decorated Officer of Legion d’Honneur, Commandeur Ordre National du Merite from France and Officer Bundes Verdienst Kreuz from Germany. He has received the W.T. and Idalia Reid Prize from SIAM in 2014.
He has an extensive research background in stochastic control, risk analysis and decision making. He has published 13 books and more than 400 papers and proceedings. He develops a comprehensive approach to Risk Analysis, to apprehend technical and socio-economic risks simultaneously. He has experience in aerospace and information technology industries. His main focus is presently in the energy sector.
Major challenges of Risk Management in industry
Abstract We present in this lecture the major challenges of Risk Management in industry, at a time when complexity intensifies. This justifies the introduction of a Risk Management culture and of a stringent risk organization in big industry, which procure very complex systems. We illustrate the discussion with a presentation of the Boeing 737 Max case study, which contains many important aspects, from which a risk management analysis can be derived, in a more concrete manner. Of course, not all aspects can be covered by a concrete case, but major ones are present.
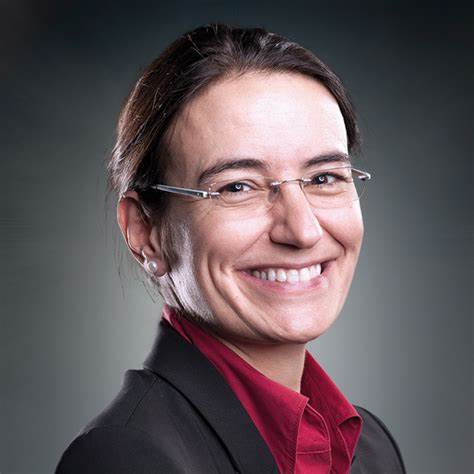
Gisela Lanza
Professor. DR.-ING. Director of Production Systems at the Karlsruhe Institute of Technology (KIT)
Go to the presentation slides
See the video of the keynote
Prof. Dr.-Ing. Gisela Lanza is member of the management board at the Institute of Production Science (wbk) of the Karlsruhe Institute of Technology (KIT). She heads the Production Systems division dealing with the topics of global production strategies, production system planning, and quality assurance. In 2009 she received the Heinz Maier-Leibnitz award of the German Research Foundation (DFG), and was awarded in 2016 with the Federal Cross of Merit on Ribbon. She is an active member of the scientific advisory board of the German Academy of Engineering Sciences (acatech) and the national platform Industry 4.0, as well as of the Steering Committee of the Allianz Industrie 4.0 Baden-Württemberg. In numerous basic and collaborative projects, Mrs. Lanza deals with the development of analytical methods for the identification and improvement of given weak points of a production system.
Enabling changeable production by utilizing digital twins
Abstract Due to the trends of individualization and mass customization, production systems and networks must be flexible and able to adapt to changing requirements. However, finding the right degree of flexibility and taking the right change measures at the right time is a difficult decision problem requiring foresight in complex environments. Digital twins can enable manufacturing companies to appropriately address this complexity by allowing for profound strategic and operational decision-making. First of all, a definition, the role and function of digital twins in the context of Industry 4.0 is provided. Second, various use cases for digital twins in production are presented. Finally, requirements are aggravated by specifying and shaping a vision of an omnipotent digital twin for the changeable factory of the future.
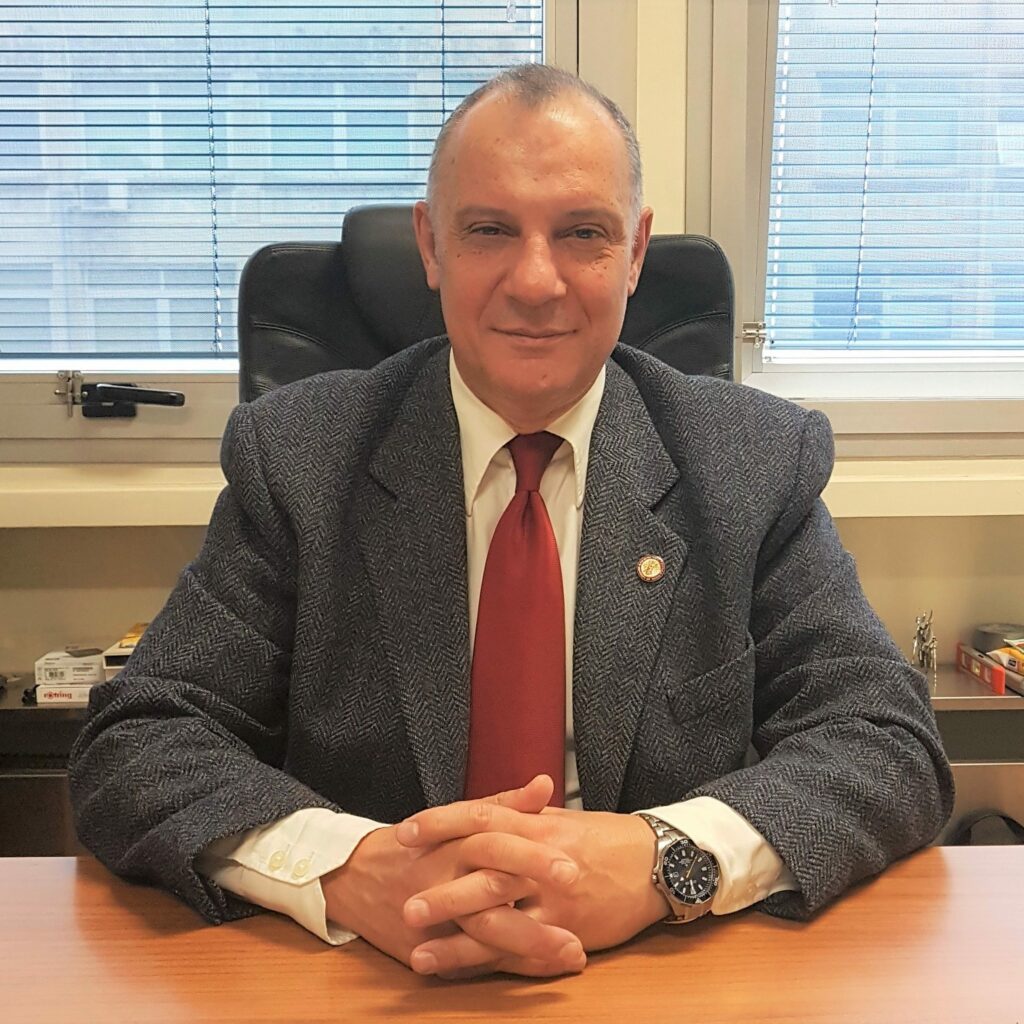
Dimitris Mourtzis
Professor of Manufacturing Systems and Director of the Laboratory of Manufacturing Systems and Automation, University of Patras
Go to the presentation slides
See the video of the keynote
Dimitris Mourtzis is a Professor in the Department of Mechanical Engineering and Aeronautics of the University of Patras, Vice President of Research and Development of University of Patras, Governing Board Member of the University of Patras at the Clean Aviation Joint Undertaking, Director of Laboratory for Manufacturing Systems and Automation and Founding Member of the Teaching Factory Competence Center. He is a Fellow of the International Academy for Production Engineering (CIRP), the International Federation of Automatic Control (IFAC) Manufacturing Modelling for Management and Control (IFAC TC5.2), the International Federation of Information Processing IFIP WG 5.7-Advances in Production Management Systems. Professor Mourtzis is member of numerous scientific associations including the American Society of Mechanical Engineers (ASME), the Society of Manufacturing Engineers (SME), the Presidential Board of the International Association of Learning Factories (IALF), the European Factories of the Future Association–EFFRA, the European Manufacturing and Innovation Research Association (EMIRACLE), the European Aeronautics Science Network / Association EASN and others. His scientific interests focus on the Design, Planning and Control of Manufacturing Systems and Networks, Robotic Systems, Automation, Augmented, Mixed, and Virtual Reality in Manufacturing, and Manufacturing Processes Modelling and Energy Efficiency. Furthermore, his research interests are also focused on the design, development and implementation of solutions based on the utilization of cutting-edge digital technologies, such as Cloud Technologies, as well as on the development of Product-Service Systems (PSS). He is also actively involved in the Digital Transformation of Manufacturing Companies and Implementation of Industry 4.0 practices. He has published more than 290 publications including refereed journal papers, editorials, book chapters and conference proceedings with a total number of more than 9.300 unique citations (h-index 49). He is also Member of the Editorial Board of several Scopus Indexed International Journals and Guest Editor in a number of Special Issues.
Artificial Intelligence for Production Management and Control towards Mass Personalization in Industry 4.0
Abstract The Mass Personalization (MP) paradigm is already a reality and has increased the involvement/engagement of end-users in the product lifecycle. It requires responsive and flexible manufacturing operations to produce cost-effective individualized products in dynamic batch sizes at scale taking into consideration the unique preferences of each customer. Therefore, modern manufacturing systems must be capable of responding quickly to changing demands and conditions in the factory, supply chain, and customer needs. However, current manufacturing systems, have not yet fully adapted to dynamic production environments by changing system configurations and production plans while maintaining stable production output. As a result, in the context of MP, a manufacturing system must be capable of self-optimizing manufacturing operations in order to achieve flexible, autonomous, and error-tolerant production. Based on the above-mentioned, the ability of a company to build effective data collection and processing methodology that orchestrate data flows, and then draw meaningful and actionable insights from them, is critical to MP success. As such, the technological drivers of MP are the Big Data Sets and Artificial Intelligence (AI) among other pillar technologies of Industry 4.0. This keynote talk aims to identify and highlight the state-of-the-art on how the integration of AI and Big Data technologies and techniques in the production management and control will contribute towards the efficient personalization of each customer’s experience under the framework of Industry 4.0 and beyond.
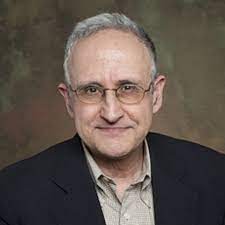
Michael Pinedo
Professor of Operations Management in the Department of Information, Operations and Management Sciences
Stern School of Business, New York University
Go to the presentation slides
See the video of the keynote
Michael Pinedo is the Julius Schlesinger Professor of Operations Management in the Department of Technology, Operations, and Statistics at New York University Leonard N. Stern School of Business. From 1982 to 1997 he taught in the Industrial Engineering and Operations Research department at Columbia University. He taught at the Instituto Venezolano de Investigaciones Cientificas (Caracas) from 1978 to 1980 and at the Georgia Institute of Technology from 1980 to 1982. Professor Pinedo received an Ir. degree in Mechanical Engineering from the Delft University of Technology in 1973, and both an M.Sc. and Ph.D. in Operations Research from the University of California at Berkeley in 1978.
Professor Pinedo's research focuses on the modeling of production and service systems, more specifically, on the planning and scheduling of these systems. Recently, his research has focused on operational risk in financial services. He has both authored and co-authored numerous technical papers on these topics. He is the author of the books Scheduling: Theory, Algorithms, and Systems (Springer), and Planning and Scheduling in Manufacturing and Services (Springer), and the coauthor of Queueing Networks: Customers, Signals and Product Form Solutions (Wiley). He is co-editor of Creating Value in Financial Services: Strategies, Operations, and Technologies (Kluwer), and editor of Operational Control in Asset Management - Processes and Costs (Palgrave/McMillan). Over the last two decades,
Professor Pinedo has been involved in industrial systems development. He supervised the design, development, and implementation of two planning and scheduling systems for the International Paper Company. He also actively participated in the development of systems at Goldman Sachs, Philips Electronics, Siemens, and at Merck.Professor Pinedo is currently editor of the Journal of Scheduling (Wiley). He is also associate editor of Management Science, associate editor of Naval Research Logistics, department editor of Production and Operations Management, associate editor of Manufacturing and Services Operations Management, and associate editor of the Journal of Operational Risk.
Scheduling Applications in Industry – Steelmaking and Micro-electronics
Abstract Efficient scheduling of industrial systems typically have a major impact on their productivity levels. In this presentation we focus on scheduling applications in two different industries, both being of importance, namely steelmaking and microelectronics. In steel production the steelmaking-continuous casting (SCC) process is a bottleneck. Its scheduling has become more challenging over the years. We first describe the modeling of the essential features of an SCC process, such as unrelated parallel machine environments, stage skipping, and maximum waiting time limits in between successive stages. The objective is the minimisation of the total weighted waiting time, total earliness, and total tardiness. The problem can be formulated as a mixed integer program and we present an iterated greedy matheuristic that solves its subproblems to find a near-optimal solution. Through numerical experiments, we show the effectiveness of such an algorithm. The microelectronics industry is conceptually very different from the steel making industry. The manufacturing processes in a wafer fab can be modeled as flow shops with re-entry, which are special cases of job shops with recirculation. The re-entries of the orders make the associated scheduling problems conceptually very difficult. We discuss the properties of the optimal schedules for various different objective functions. We conclude this presentation with various other scheduling applications in industry that deserve research attention.
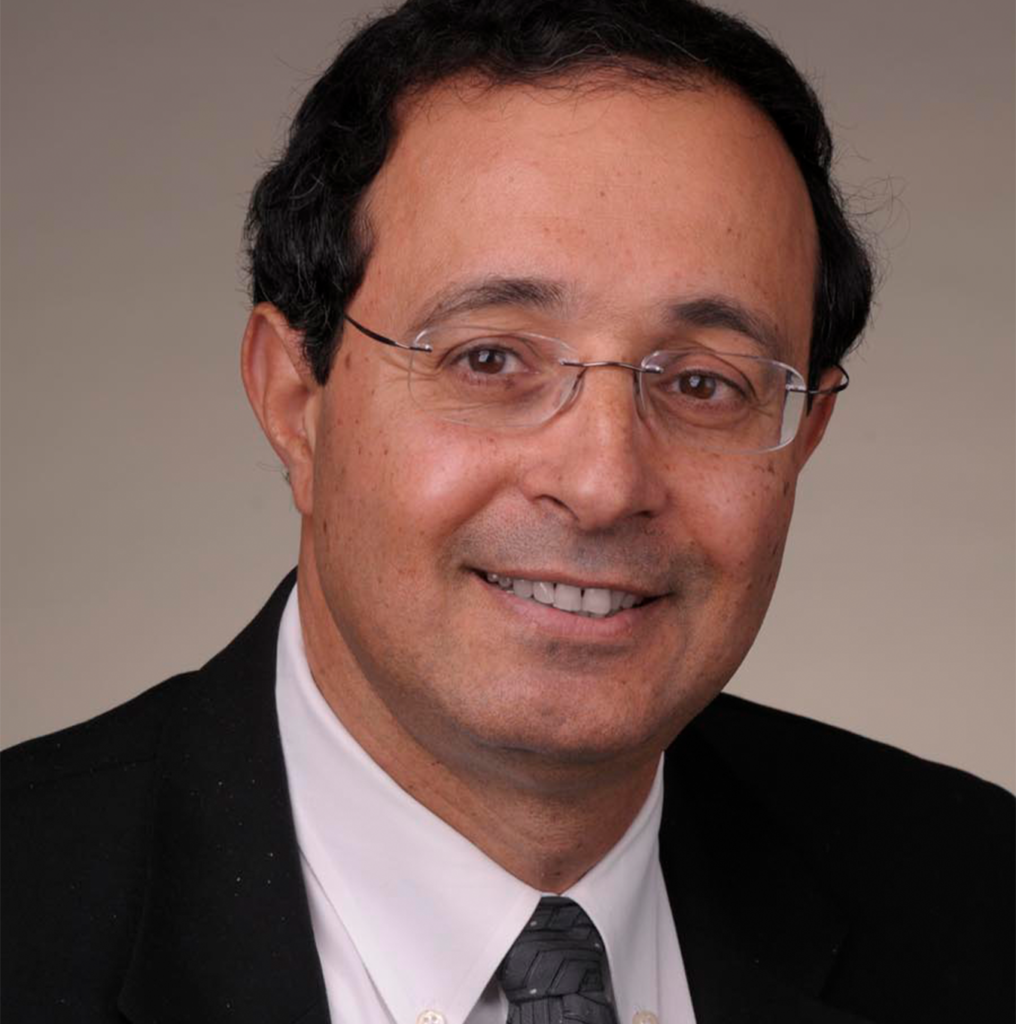
David Simchi-Levi
Professor of Engineering Systems & Director of the Data Science Lab
MIT
Go to the presentation slides
See the video of the keynote
David Simchi-Levi is a Professor of Engineering Systems at MIT and serves as the head of the MIT Data Science Lab. He is considered one of the premier thought leaders in supply chain management and business analytics.
Professor Simchi-Levi is the current Editor-in-Chief of Management Science, one of the two flagship journals of INFORMS. He served as the Editor-in-Chief for Operations Research (2006-2012), the other flagship journal of INFORMS and for Naval Research Logistics (2003-2005). He is an INFORMS Fellow, MSOM Distinguished Fellow and the recipient of the 2014 INFORMS Daniel H. Wagner Prize for Excellence in Operations Research Practice; 2014 INFORMS Revenue Management and Pricing Section Practice Award; 2009 INFORMS Revenue Management and Pricing Section Prize and Ford 2015 Engineering Excellence Award. He was the founder of LogicTools which provided software solutions and professional services for supply chain optimization. LogicTools became part of IBM in 2009. In 2012 he co-founded OPS Rules, an operations analytics consulting company. The company became part of Accenture in 2016. In 2014, he co-founded Opalytics, a cloud analytics platform company focusing on operations and supply chain intelligence. The company became part of the Accenture Applied Intelligence in 2018.
From Data to Science and Back
Abstract In this talk I will describe my journey in the applications of data science to operations. I will start by showing how the development of personalized offering in the airline industry led to a new statistical learning method. We than describe how a new approach for experimental design generated data that allowed the evaluation of machine learning based pricing algorithm. Finally, we show how pre-pandemic research generated significant impact during the pandemic by allowing companies to increase supply chain resiliency.